Capabilities
At NES, we pride ourselves on our innovative and proactive approach to elastomeric sealing solutions. Our robust research and development programme underpins all our activities, allowing us to constantly explore new techniques and develop cutting-edge compounds.
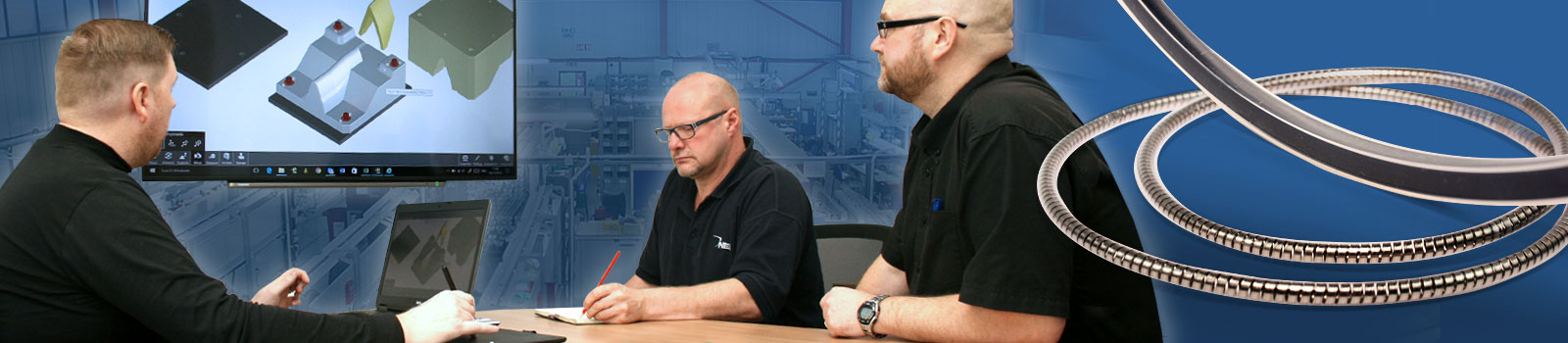
Delivering Comprehensive Elastomeric Sealing Solutions Tailored to Your Needs
Extensive Capabilities
Our wide-ranging capabilities encompass:
End-to-end solutions, from concept to realisation
Rapid prototyping for efficient product development
In-house FEP/PFA Teflon™ extrusion, paired with in-house elastomeric core extrusion for seamless NES Ncaps® manufacturing
Expertise in bonding rubber to various substrates, including PTFE, PEEK, titanium, stainless steel, aluminium, and brass
In-house tooling and grinding capabilities for smooth finishes and ultra-tight tolerances
Manufacture of VulcOrings, custom profiles, and inflatable seals using a parent material and a 45-degree join for optimal material characteristic preservation and bond strength
Availability of BS, AS, and JS standard sizes, as well as bespoke options
ISO 7 cleanroom moulding and extruding for uncompromised hygiene
ISO 6 cleanroom packaging to maintain product integrity
All NES products undergo stringent testing before delivery. Our TECHNIFLATE® inflatable seals, for instance, are tested at 1 bar (unsupported) to ensure quality and minimise the risk of failure.
We understand that our customers often require quick turnarounds, and we are committed to delivering unparalleled quality without compromising on speed.
Our strong partnerships with trusted outsourced vendors, a dedicated Materials Manager focused on compound development, and an experienced Technical Engineering department enable NES to provide comprehensive and integrated solutions tailored to your needs.
-
Polymers Science
NES’ expertise in material behaviour ensures that we can design and develop solutions that exceed the most demanding technical requirements.
Our products utilise custom and proprietary compound formulations which have been developed and refined over many years by NES’ technical team; resources include over 350+ different rubber compound grades and we are constantly developing new materials to meet specific technical requirements.
Chemical validation to specifications
Physical validation to specifications
Colour matching
Industry certifications and approvals where appropriate
-
Rubber to Metal Bonding
At NES, we’ve honed our rubber to metal bonding capabilities over many years, working with a wide range of metal and rubber materials. Thanks to our close collaborations with key customers, we’ve even developed a line of rubber and titanium components specifically tailored to the demanding requirements of the semi-con industry.
Our expertise in mould-tooling development, surface preparation processes, primer selection, and curing configuration – including temperature, pressure, and duration – has earned us a solid reputation in markets that demand strong rubber to titanium bonding, such as the wider semi-con and aerospace & defence industries.
Utilising the skill of our inhouse engineering team to overcome the natural incompatibility of rubber and metal, NES achieves components which attain tight dimensional tolerances and are strong enough to withstand stringent dynamic and static (destructive) testing.
We take pride in our commitment to quality control, carefully matching each component to a full set of recorded measurement data and thoroughly cleaning it in our clean-room packing environment prior to shipping. If you’re looking for a trusted partner for rubber to metal bonding, look no further than NES.
-
Sub Assembly
NES takes pride in producing the best custom sub-assembled parts for our customers. We offer an extensive range of sub-assembly components, including ducting for environmental control systems and auxiliary power units (APUs).
Our engineered approach allows us to develop products with single architecture to multi-branch architecture, using our highly skilled hand fabrication techniques. This approach enables us to deliver products that meet our customers’ unique requirements, ensuring their complete satisfaction.
Our extensive sub-assembly facilities are located within a clean environment, which allows us to maintain the highest standards of quality and precision. This environment also enables us to offer products that exceed our customers’ expectations, setting us apart from our competitors.
Whether you’re in need of custom sub-assembled parts or standard components, you can trust NES to deliver exceptional quality and service.
-
Special Moulding
At NES, we take pride in our ability to produce custom-made special mouldings using our in-house moulding facilities. Our state-of-the-art facilities are capable of manufacturing small micro mouldings that are just a few millimetres in size, as well as large mouldings with a size range up to 1000mm.
Our moulded seals are used in a wide range of different markets, including the semi-con, aerospace, defence, pharmaceutical, and many others. This diverse application speaks to the versatility and adaptability of our products.
We use specially formulated elastomers tailored to exact project requirements to fabricate our moulded seals. This ensures that our seals can operate in the most demanding of environments, including vacuum, high pressure, extreme hot or cold, and fuel or chemically corrosive environments.
With NES, you can trust that you’re getting a high-quality, custom solution that will meet your specific needs, regardless of the industry or application.
-
Extrusion
With a highly developed in-house extrusion production facility, extruded seals are a particular area of expertise for NES. We offer a wide range of extruded seals across various profiles and using different rubber compounds. Our areas of specialisation include colour matching and flame-retardant materials.
We manage our extrusion production facility in the same way as an external supplier, ensuring that our extrusion production keeps pace with other production requirements. Our extruded seals are used in the OEM and MRO sectors, with applications ranging from aircraft baggage door seals and cockpit window seals to galley seals and spoiler seals in the aerospace industry.
At NES, we take pride in our ability to produce high-quality seals that are fabricated from specially formulated elastomers tailored to exact project requirements. This allows our seals to perform in demanding and varied environments, including vacuum, high pressure, extreme hot or cold, and fuel and chemically corrosive environments.
Uniquely, we’re able to produce high-quality seals as small as 1.08mm and as large as 70.00mm in cross-section, ensuring that we can meet our customers’ unique requirements, regardless of size or complexity. With NES, you can trust that you’re getting a custom solution that is of exceptional quality and developed to meet your specific needs.
-
Tubing Made from Teflon™
At NES, we pride ourselves on our ability to produce high-quality tubing made from Teflon™. Thanks to our in-house and highly developed extrusion production facility, we’re able to extrude the jacket as well as the elastomeric core for our NES NCAP® encapsulated seals. This allows us to maintain full dimension control, with a zero tolerance for air gaps, mitigating failure risk and enhancing compression set performance.
Our Teflon™ tubing is used both as a component to an NES NCAP® encapsulated seal and as a standalone product. We use only the highest quality materials, ensuring that our Teflon™ tubing is of the utmost durability and reliability.
Our experienced and highly skilled team ensures that our Teflon™ tubing meets and exceeds our customers’ expectations. With NES, you can trust that you’re getting a custom solution that is developed to meet your specific needs and that is of the highest quality.
-
CAD/DPD & Bespoke Engineering
NES understands the importance of being easy to work with, which is why we offer a ‘start to finish approach’ that involves working closely with our customers throughout the entire process.
Using CAD (Computer Aided Design) and DPD (Distributed Participatory Design), we proactively assist with product development, refinement, and ‘trouble-shooting’, ensuring that our customers get the solutions they need, quickly and efficiently.
Our Product Development team has extensive experience, working with customers on diverse projects with unique challenges. As a major exporter, we’re accustomed to and comfortable with dealing with development challenges arising from different geographical areas.
NES is equipped to read drawings in a range of formats, including STP, IGES, ACIS, STL, CGR, DXF, and SWG. This allows us to work seamlessly with our customers, regardless of the tools or formats they use.
-
Testing & Evaluation
NES is committed to pushing the boundaries of our expertise and enhancing our processes, which is why we believe in putting ourselves to the test.
Our in-house testing facilities are rigorous and exhaustive, providing customers with enhanced development support during co-development projects and ensuring peace of mind regarding the quality and performance of our products.
We employ a range of testing processes, including:
SG testing
Indentation testing to ASTM Shore A
Elongation at break testing
MPA testing
Stress testing
Peel testing
Immersion testing
Compression set testing
Oil immersion testing
Heat age testing
Pressure testing
Submerged cycle inflation testing
Non-submerged cycle inflation testing
Destruction testing
At NES, we take pride in our commitment to quality control, ensuring that our products meet the highest standards of reliability and durability. With our rigorous testing processes and exceptional expertise, you can trust NES to deliver products that exceed your expectations.